Home About the Company Press and Media News Tatra Trucks and partners develop and test new Tatra Force with automated steering system
Tatra Trucks and partners develop and test new Tatra Force with automated steering system
4 October, 2023
In addition to the development and production of standard truck model lines, Tatra Trucks also develops alternative drives and other modern technologies for vehicles. It is therefore also involved with its partners in research in the field of automated vehicle control and the development of the necessary software.
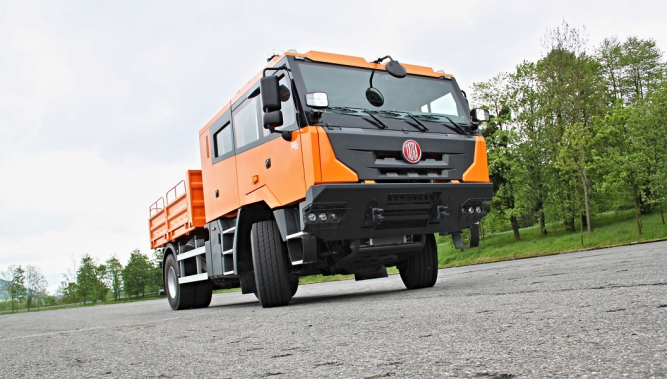
View fotogallery
Development of automated steering for Tatra vehicles in three phases
On the Tatra Trucks test polygon, it is currently possible to see a Tatra Force vehicle in which the driver does not sit in the cab when driving, but is controlled by an operator using a remote control. It is a prototype of an automated driving (AD) vehicle. The project is divided into three phases, with the first phase currently underway, which is the validation of the systems. The final goal of the project is to produce a Level 3 truck with automated driving capable of autonomous driving. The prototype, currently being tested with remote control, is a preview of vehicles that may find use with rescue units and in industry.
The first phase of the project involves integrating sensors into the vehicle and making the turn assist and passive lane change assistant operational. In the second phase, the vehicle will be equipped with Lidar for informative obstacle detection. In the third phase, the sensors will use the implemented software and hardware interfaces to steer the vehicle itself, control the speed of the vehicle, the engine or the functions of the transmission and braking system, etc. In addition, this will enable the operation of other advanced driver assistance systems (ADAS) such as adaptive cruise control, emergency braking and lane change assistants, etc.
The prototype has also been developed from the outset for use in specific conditions, taking into account the typical operating environment of Tatra vehicles. "We are trying to develop a vehicle prepared for the most difficult operating conditions, where Tatra trucks are commonly used, so it must have, for example, sensors with higher resistance or a cyber security system. It is the consideration of operation in difficult terrains or for users with high demands that is the main advantage of the Tatra solution compared to other automated vehicle control systems. For example, rescue and fire brigades are increasingly demanding vehicles with automated steering or remote control, which could be sent unmanned into hazardous areas. Such a Tatra vehicle, which can also be equipped with an armoured cab protecting the automated driving system, could be accompanied by an unmanned flying vehicle to help navigate in dangerous and risky areas. Other applications for Tatra vehicles with automated steering could be found in closed industrial and mining areas," explained Radomír Smolka.
Cooperation between industry and academia
The Mobility Lab team from the VSB-TUO University and Valeo are working together with the Tatra Trucks on the project to implement the automated system in the latest third-generation Tatra Force. In addition to experts, the project involves a number of doctoral and master's students as junior researchers. The development of the vehicle runs from 2021, with the intention of implementing sensors as well as software control and assistance systems in the truck so that higher levels of driving automation can be implemented in different driving modes. The truck will be used as a technology demonstrator, contributing to the development of the market for advanced driver assistance systems (ADAS) and automated driving systems (AD) developed and manufactured in the Czech Republic.
"Tatra Trucks has prepared for the project the Tatra Force, the latest third generation vehicle, which had its premiere in spring this year. The new generation of the Tatra Force model range is equipped with modern electronic systems that are essential for implementing elements of autonomous driving," explained Radomír Smolka, the Tatra Trucks director of research and development, adding: "These include electronic systems for vehicle and engine control, as well as equipment common in passenger cars that meets current safety standards, such as emergency braking, blind spot monitoring, pedestrian monitoring, etc. The car is powered by a 291 kW Cummins L9 power unit coupled to an Allison 4500P transmission with retarder."
"Valeo is responsible for the integration of sensor elements such as ultrasonic, radar, laser or camera sensors in the Tatra automated driving project, as well as for the subsequent processing of the control algorithms. Valeo has a development centre that employs around 700 development staff, of which around 600 work specifically on the development of automated driving systems. In addition, we have a group that defines, develops and integrates automated driving systems for trucks," said Tomáš Vajdiak and Lukáš Čarek, Valeo's R&D managers.
Another partner, Mobility Lab VSB-TUO, is in charge of developing the interface of the entire system, which will enable autonomous movement of the Tatra in various situations. "Our Mobility Lab specialises in teaching, developing and researching technical software and hardware tools for automated driving of cars, trucks, public transport vehicles and industrial vehicles. It is therefore very experienced in this respect," said Petr Šimoník, Vice Dean for Cooperation with Industry at VSB-TUO.
Data communication interface for automated control
The Tatra Force prototype is already equipped with full sensor equipment and has a Drive by Wire Truck Interface, and servers are also available for data collection. The 1st generation Drive by Wire Truck Interface is an important element of the automated driving system, as it ensures two-way transmission of requests and data between the autonomous driving assistants or algorithms and the vehicle's basic electronic systems (drive, transmission, servo control, brakes and infotainment).
"Drive by Wire Truck Interface is a sophisticated data controller that enables the transmission of control commands and information data to stimulate vehicle systems in automated driving. It enables comprehensive control of the vehicle in longitudinal and lateral directions, including the ability to control and co-operate friction and supplementary braking (retarder), shifting and activation of special comfort, signalling and information functions," explained Petr Šimoník, adding: "In order to ensure autonomous driving, the vehicle must be equipped not only with this sophisticated interface, but also with domain control systems and sensor systems for environmental monitoring, object recognition and the implementation of strategies or control and regulation algorithms for automated driving."
The Drive by Wire Truck Interface 1st Generation represents an important stage of development to deliver a concrete and practical system that provides assistance in, for example, parking or complex manoeuvring, but also the ability to provide autonomous driving for higher levels of driving automation. The interface validation also included the possibility of Truck Remote Control. The developed interface currently serves as a starting point for developers to implement specific algorithms and experimental tests, or control of the vehicle's electronic systems in lower and higher levels of autonomy.